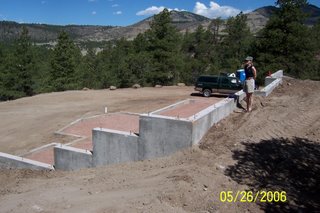
This has been a busy last few days in that Johnny's completed the initial plumbing work, Rick's Pump Service ran the lines and wiring for the well-cistern-house water piping and there were a couple of inspections; state plumbing and electrical.
After all of that was completed Tim came back in and backfilled EVERYTHING, he also leveled the area around the house and set a number of big rocks along the outside edge of the driveway. The area in front of the house will ultimately be a concrete patio colored to match the surrounding ground. It looks really good.
My 86 (87 next month) year old Dad, Tom Caulfield, was in town over the weekend for Derek's Graduation,

We are real proud of Derek who graduated with an Honor Cord from the National Art Honor Society.
He leaves for Italy next week for about 10 days and will be attending Western State College in Gunnison next August.
It has been two years since the last time my Dad visited and as he mentioned last time, as now, that it is hard to really understand the scope of the area just seeing it in photographs. Maybe we can talk him into visiting again this year when the house is done.
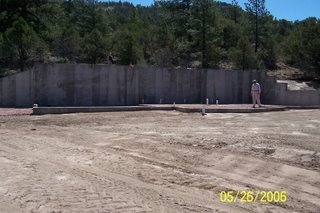
The white pipes that you see sticking up are the drain plumbing that will end up under the concrete slab floor. They are all capped for now and will be trimmed to length when the rough plumbing is done after the framing is completed.
We did a couple of test ourselves while there; one was to park the truck in the garage and the other was to look at the south wall for the location of the back bedroom window.

The truck fit fine.
Still unsure about the bedroom window, but that will be looked at on Tuesday. It could mean some work with a concrete saw before the framing.

I know many folks think that I am nuts to be looking at the schedule so closely, but I just like to know when I am behind the power curve, and if so how much, and why. For those keeping score, we are 14 days behind right now. This is almost entirely due to additional time taken up in the design stage. BUT, if we make the framing start date on June 5 we will be back on the timeline set last November.
I heard an interesting comment on an edition of "This Old House" this morning. Kevin the host said of a project that had just finished framing, "that it would be done in no time", and Tom Silva said that once framed, a project was only 1/3 done, and the final 2/3's takes a lot more time to complete. Well, we haven't even gotten to that point, so it will be a interesting summer. The days and weeks seem to be flying by since we started and I hope we can keep the momentum as we get into the body of the build.
Next weekend we will be chipping up the tree that were cut for the house clearing and removing the "doghouse from the well head. A couple of folks have tried to pull it off and someone finally succeeded in breaking the high quality "through the top" plumbing I had installed back in '99. Lucky for us Mike Sellen, across the way, came over and fixed it before we even knew there was a problem. Thanks, Mike we owe you one. Autumn Creek really is made up of a great group of people.