
Tim is the the kind of sub you want working with you, as I called him Monday night to give him the latest schedule and he was ready with suggestions in how we could work through all of the steps we needed to complete in the next couple of weeks. AND he was there this morning at 8am to make sure we were both on the same page, AND he suggested snapping chalk lines for the waterproofing. He seems to think a number of steps ahead of me, which I believe will make a big difference once the house starts to frame up and the site gets crowded.
Tim is going to run the sewage line to the septic system tomorrow. He also had me call Rick's Pump Service about getting the water line and wiring layed before he backfills around the walkout walls. I had been wondering when we were going to do this and if I might be trenching the same trench twice. So then we will be set for the pitless adapter installation, and cistern with a keep full float system to be installed once the house is weathered in.
Tim will also do the backfill on the floor to get things ready for the plumbers on Monday.
Emily at Johnny's Plumbing (she is a gem to work with also) has scheduled the underslab pumping work for Monday (5/22), with the State inspection on Tuesday or Wednesday. This should set up well for Tim to get back in week after next to pour the slab and deck piers.
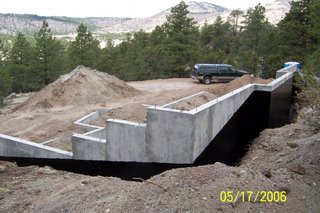
I over estimated the amount I needed by two pails (10 gal), which I figure was due to computing the step down wall as a rectangle and the margin from the top of the walls to conceal the waterproofing below the final grade. This was important because I wanted to make sure that my application rate met the specs on the product.
Now the real dirt on the waterproofing. I knew going in this was going to be messy, but I had no idea. I wore disposable coveralls over my clothes and heavy duty latex gloves to control the clean-up...Yah right. By the time I was done my gloves had to a great extent become glued to the extension pole on the roller (that whole application rate thing sounded pretty good right up to now) and the coveralls were useless as the asphalt waterproofing went right through them.
So picture this, I am in a trench 2-3' wide and 3' to 7' feet deep with dirt piled high on the outside. The sun is out and blazing (remember this is 8400' MSL) and I realize that bees seem to be attracted to this stuff. Oh yah, there is NO wind, breeze, etc., so the fumes from the asphalt is sitting in the trench with me.
By the time I was done, nauseousness had pretty much set in, I was sunburned and probably dehydrated, because I didn't want to take off the grimy, gummy, smelly gloves to open a bottle of water during this whole ordeal.
But wait, I wasn't done. Now I got to wrangle 100' lengths of 4" diameter stiff plastic tubing into this trench. I am sure there is an "approved" way of doing this, but I missed that life lesson. On the first roll I thought I could lay it out straight and then pull it in. Nice idea, but houses have corners and this stuff didn't want to go around them without personal coaxing from the crew. Did I mention the crew was Pat, and his merry band of man, "count off, one, all here". So it was back and forth moving this 100' inchworm around the house.
Being the smart guy I am. I deduced that there had to be a better way. So with the next roll I thought I would roll it out in the trench. These are rolls about 3' thick and 4' in diameter and remember the trench is 2-3' wide. So now instead of the inchworm, it was python rass'lin.
I had by this point sweated through clothes, overalls, but not the gloves. I was surprised that sweat didn't pour out of them when I would lift my hands, they were that squishy.
SO finally the two ends were brought together in some type of unholy union using a connector that I luckily picked up last night.
Now I would get the opportunity to go back over the entire 200' of French Drain and cover it in water permeable cloth to keep dirt from clogging the slits in the drain pipe. Of course these rolls were 4' wide and by now the floor of the trench was getting pretty crowded with the goopy puddles of waterproofing that didn't make the wall, the drain pipe and moi (French Drain). When (not if) I touched the wall the stuff would leave a asphalt kiss. When (again not if) I would touch the dirt side of the trench a little shower of dirt would rain down, normally this would be down my collar, via my back and directly deposited in my shorts. Yah, I was ready for this to be over, but it wasn't.
Did you know that acetone will not remove asphalt. But it sure opens the pores so that when you put goof-off on (which does remove the asphalt) you get a real nice burning stinging sensation. No matter how you try you end up cleaning everything 2, no 3 , I lost count and gave up. I still had some on my face when I got home this evening.
Enough for tonight. On to the next adventure in house build!
1 comment:
So Pat, did this adventure satisfy you need to be responsible for part of the construction? Isn't paying for it enough?
So how much did you save doing it yourself?
And how are you going to ever show someone your contribution to the actual construction?
But then again, the worst day at the construction site of your dream home is better than a good day at work!
I am enjoying your progress, you may want to consider becoming a GC in your next life!
Post a Comment